1,554 resources related to
Design For Manufacture
Read more
Featured Article
Read more
Top Conferences on Design For Manufacture
2023 IEEE International Symposium on Circuits and Systems (ISCAS)
2023 IEEE International Instrumentation and Measurement Technology Conference (I2MTC)
2022 35th International Conference on VLSI Design and 2022 21st International Conference on Embedded Systems (VLSID)
2022 IEEE Custom Integrated Circuits Conference (CICC)
2021 International Conference on IC Design and Technology (ICICDT)
2021 IEEE 14th International Conference on ASIC (ASICON)
2021 IEEE 48th Photovoltaic Specialists Conference (PVSC)
2021 IEEE International Conference on Plasma Science (ICOPS)
2020 IEEE International Conference on Robotics and Automation (ICRA)
2020 22nd European Conference on Power Electronics and Applications (EPE'20 ECCE Europe)
2020 IEEE Nuclear Science Symposium and Medical Imaging Conference (NSS/MIC)
2019 IEEE Energy Conversion Congress and Exposition (ECCE)
2018 13th World Congress on Intelligent Control and Automation (WCICA)
2018 IEEE Sensors Applications Symposium (SAS)
2018 IEEE 18th International Power Electronics and Motion Control Conference (PEMC)
2018 International Conference on Reconfigurable Mechanisms and Robots (ReMAR 2018)
2018 35th National Radio Science Conference (NRSC)
2018 IEEE PES Asia-Pacific Power and Energy Engineering Conference (APPEEC)
2018 IEEE Power & Energy Society Innovative Smart Grid Technologies Conference (ISGT)
2018 IEEE 42nd Annual Computer Software and Applications Conference (COMPSAC)
2017 IEEE International Conference on Robotics and Biomimetics (ROBIO)
2017 American Control Conference (ACC)
2016 IEEE International Symposium on Assembly and Manufacturing (ISAM)
2016 3rd International Conference on Systems and Informatics (ICSAI)
2016 Future of Instrumentation and Internet Workshop (FIIW)
2015 14th International Conference on Computer-Aided Design and Computer Graphics (CAD/Graphics)
2014 IEEE International Electric Vehicle Conference (IEVC)
2013 International Conference on Mechatronic Sciences, Electric Engineering and Computer (MEC)
2013 IEEE/ACM International Conference on Computer-Aided Design (ICCAD)
2012 International Conference on Computational Intelligence and Software Engineering (CiSE)
2012 International Conference on Management and Service Science (MASS 2012)
2012 3rd International Conference on Mechanic Automation and Control Engineering (MACE)
2012 3rd International Conference on E-Business and E-Government (ICEE)
2011 3rd IEEE International Conference on Information Management and Engineering (ICIME)
2011 IEEE 6th International Workshop on Electronic Design, Test and Application (DELTA)
2011 IEEE 12th International Conference on Computer-Aided Industrial Design & Conceptual Design (CAID & CD)
2010 3rd International Conference on Business Intelligence and Financial Engineering (BIFE)
2010 International Conference on Future Information Technology and Management Engineering (FITME)
2010 International Conference on Computer Application and System Modeling (ICCASM 2010)
2010 International Conference on Computer Science and Software Engineering (CSSE 2010)
2010 3rd International Conference on Computational Intelligence and Industrial Application (PACIIA)
2010 2nd International Conference on Industrial and Information Systems (IIS 2010)
2010 International Conference on Intelligent Computation Technology and Automation (ICICTA)
2007 Seminar for Advanced Industrial Control Applications (SAICA)
More links
Top Videos on Design For Manufacture
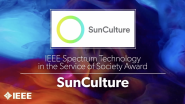
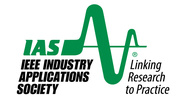
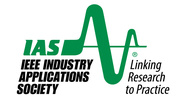
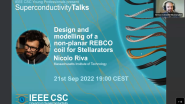
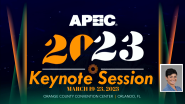