287 resources related to
Wafer Technology
Read more
Featured Article
Read more
Related topics
No topics related to "Wafer Technology"
Top Conferences on Wafer Technology
2022 IEEE Photonics Conference (IPC)
2022 IEEE International Interconnect Technology Conference (IITC)
2021 International Semiconductor Conference (CAS)
2021 IEEE 71st Electronic Components and Technology Conference (ECTC)
2021 32nd Annual SEMI Advanced Semiconductor Manufacturing Conference (ASMC)
2021 IEEE International Ultrasonics Symposium (IUS)
2021 IEEE 48th Photovoltaic Specialists Conference (PVSC)
2021 IEEE 16th International Conference on Nano/Micro Engineered and Molecular Systems (NEMS)
2021 International Conference on IC Design and Technology (ICICDT)
2020 IEEE Nuclear Science Symposium and Medical Imaging Conference (NSS/MIC)
ESSDERC 2020 - IEEE 50th European Solid-State Device Research Conference (ESSDERC)
2019 IEEE 9th International Nanoelectronics Conferences (INEC)
2019 IEEE 15th International Conference on Automation Science and Engineering (CASE)
2019 22nd European Microelectronics and Packaging Conference & Exhibition (EMPC)
2018 15th International Conference on Electrical Engineering/Electronics, Computer, Telecommunications and Information Technology (ECTI-CON)
2018 IEEE 38th International Electronics Manufacturing Technology Conference (IEMT)
2017 American Control Conference (ACC)
2017 18th International Conference on Thermal, Mechanical and Multi-Physics Simulation andExperiments in Microelectronics and Microsystems (EuroSimE)
2017 30th International Vacuum Nanoelectronics Conference (IVNC)
2017 IEEE Bipolar/BiCMOS Circuits and Technology Meeting - BCTM
2017 IEEE International Meeting for Future of Electron Devices, Kansai (IMFEDK)
2017 European Conference on Circuit Theory and Design (ECCTD)
2016 IEEE International Conference on Semiconductor Electronics (ICSE)
2015 8th International Congress on Image and Signal Processing (CISP)
2015 25th International Crimean Conference "Microwave and Telecommunication Technology" (CriMiCo)
2014 IEEE Semiconductor Wafer Test Workshop (SWTW 2014)
2012 Conference on Optoelectronic and Microelectronic Materials & Devices (COMMAD)
2011 IEEE 6th International Workshop on Electronic Design, Test and Application (DELTA)
2011 China-Japan Joint Microwave Conference (CJMW)
2009 IEEE International Conference on Electro/Information Technology (eit2009)
More links
Top Videos on Wafer Technology
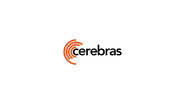
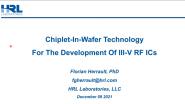


