242 resources related to
Mechanical Stress Analysis
Read more
Featured Article
Read more
Top Conferences on Mechanical Stress Analysis
2024 46th Annual International Conference of the IEEE Engineering in Medicine and Biology Society (EMBC)
2023 22nd IEEE Intersociety Conference on Thermal and Thermomechanical Phenomena in Electronic Systems (ITherm)
2022 IEEE Nuclear Science Symposium and Medical Imaging Conference (NSS/MIC)
2022 IEEE Canadian Conference on Electrical and Computer Engineering (CCECE)
2021 IEEE 11th Annual International Conference on CYBER Technology in Automation, Control, and Intelligent Systems (CYBER)
2021 IEEE 71st Electronic Components and Technology Conference (ECTC)
2021 IEEE International Symposium on the Physical and Failure Analysis of Integrated Circuits (IPFA)
2021 IEEE International Ultrasonics Symposium (IUS)
2021 International Conference on Simulation of Semiconductor Processes and Devices (SISPAD)
2021 24th International Conference on Electrical Machines and Systems (ICEMS)
2019 IEEE International Conference on Industrial Technology (ICIT)
2019 Prognostics and System Health Management Conference (PHM-Paris)
2019 IEEE Holm Conference on Electrical Contracts
2018 10th International Conference on Integrated Power Electronics Systems (CIPS)
2018 IEEE International Interconnect Technology Conference (IITC)
2017 IEEE Regional Symposium on Micro and Nanoelectronics (RSM)
2017 IEEE Electrical Design of Advanced Packaging and Systems Symposium (EDAPS)
2016 IEEE Conference on Electromagnetic Field Computation (CEFC)
2016 International Symposium on Power Electronics, Electrical Drives, Automation and Motion (SPEEDAM)
2016 Symposium on Piezoelectricity, Acoustic Waves, and Device Applications (SPAWDA)
2015 11th International Conference on Natural Computation (ICNC)
2014 Annual Oak Ridge National Laboratory Biomedical Science and Engineering Center Conference (BSEC)
2014 Joint Rail Conference (JRC)
2013 IEEE 15th International Symposium and Exhibition onAdvanced Packaging Materials (APM)
2012 International Conference on Computational Intelligence and Software Engineering (CiSE)
2012 2nd International Conference on Electronic & Mechanical Engineering and Information Technology (EMEIT)
2012 International Conference on Biomedical Engineering and Biotechnology (iCBEB)
2012 3rd International Conference on Mechanic Automation and Control Engineering (MACE)
2012 2nd International Conference on Electric Technology and Civil Engineering (ICETCE)
2012 IEEE/ASME 8th International Conference on Mechatronic and Embedded Systems and Applications (MESA)
2011 3rd IEEE International Conference on Information Management and Engineering (ICIME)
2011 International Conference on Multimedia Technology (ICMT)
2011 International Conference on Transportation and Mechanical & Electrical Engineering (TMEE)
2011 2nd International Conference on Artificial Intelligence, Management Science and Electronic Commerce (AIMSEC)
2011 International Conference on Artificial Intelligence and Computational Intelligence (AICI)
IECON 2011 - 37th Annual Conference of IEEE Industrial Electronics
2011 IEEE 12th International Conference on Computer-Aided Industrial Design & Conceptual Design (CAID & CD)
2010 3rd International Conference on Advanced Computer Theory and Engineering (ICACTE 2010)
2010 Frontiers in Automobile and Mechanical Engineering (FAME)
2010 International Conference on Computer, Mechatronics, Control and Electronic Engineering (CMCE 2010)
2010 2nd International Conference on Industrial Mechatronics and Automation (ICIMA 2010)
2010 International Conference on Computer Application and System Modeling (ICCASM 2010)
2010 International Conference on E-Product E-Service and E-Entertainment (ICEEE 2010)
2009 15th IFAC Symposium on System Identification (SYSID 2009)
More links
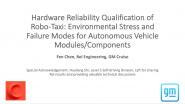
Xplore Articles related to Mechanical Stress Analysis
Periodicals related to Mechanical Stress Analysis
Visualization and Computer Graphics, IEEE Transactions on
More links